Innovation and technology at Foseco
How does the foundry industry succeed in an unpredictable and increasingly demanding market? Discover how innovation and new technologies are helping foundries navigate the storms.
We live in interesting times: times of competing priorities and new challenges. Issues that would be familiar to foundry workers of all ages – quality, yield, and cost – remain as vital today as they have always been. But they are taking on additional weight and complexity in light of new challenges around sustainability and decarbonization.
Business survival – let alone success – in this environment requires the ability to see the problems ahead and ensure solutions are ready today. Which is what we at Foseco have been doing for more than 80 years – and continue to do today.
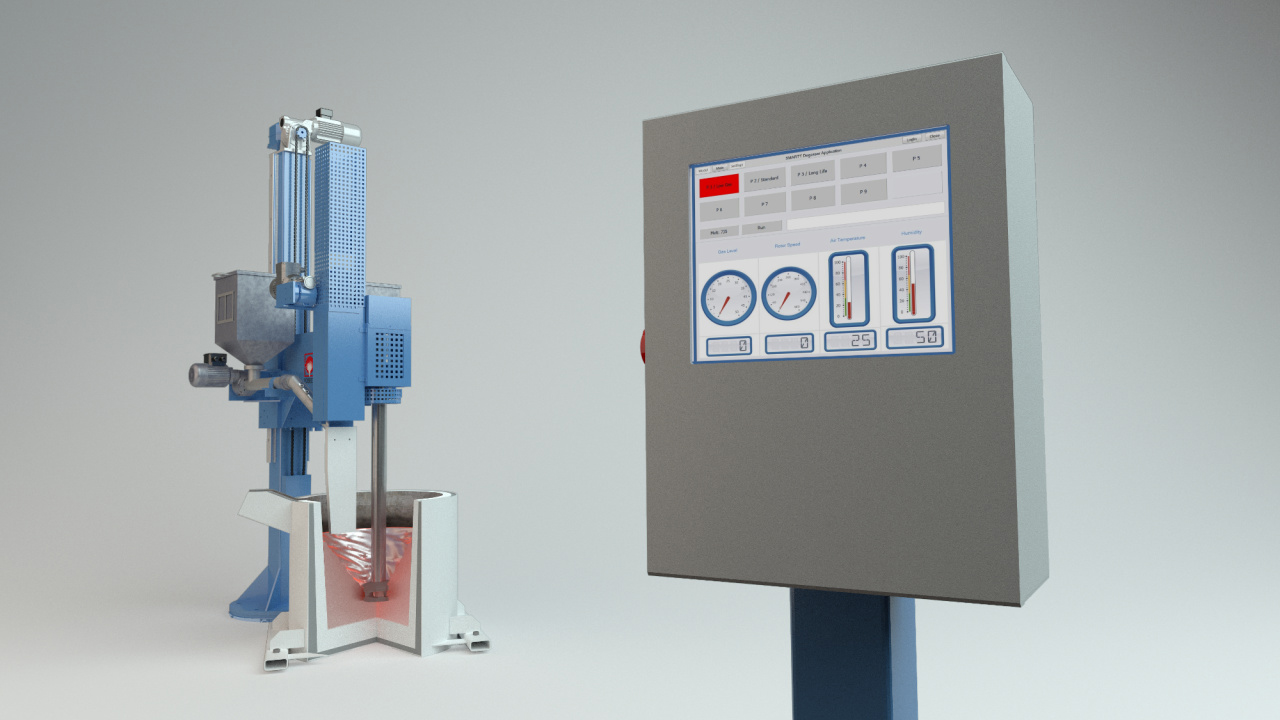
SMARTT degassing software
Technologies like our SMARTT software, which optimises rotary degassing of aluminium melts with a Foseco FDU MTS degassing unit. Based on a range of factors, including ambient conditions, melt temperature, rotor design, and alloy composition, the SMARTT software is able to predict the best treatment practice. The treatment parameters – e.g., rotor speed, inert gas flow rate, treatment time – are then automatically transferred to the FDU MTS.
The SMARTT software ensures that any defined hydrogen levels are reached through a combination of degassing and subsequent up-gassing (as needed). By ensuring optimum degassing parameters, it also reduces inert gas consumption and helps to extend the lifetime of graphite consumables. All treatment parameters are recorded and accessible via a user-friendly interface. Data can also easily be exported to standard office applications for further analysis.
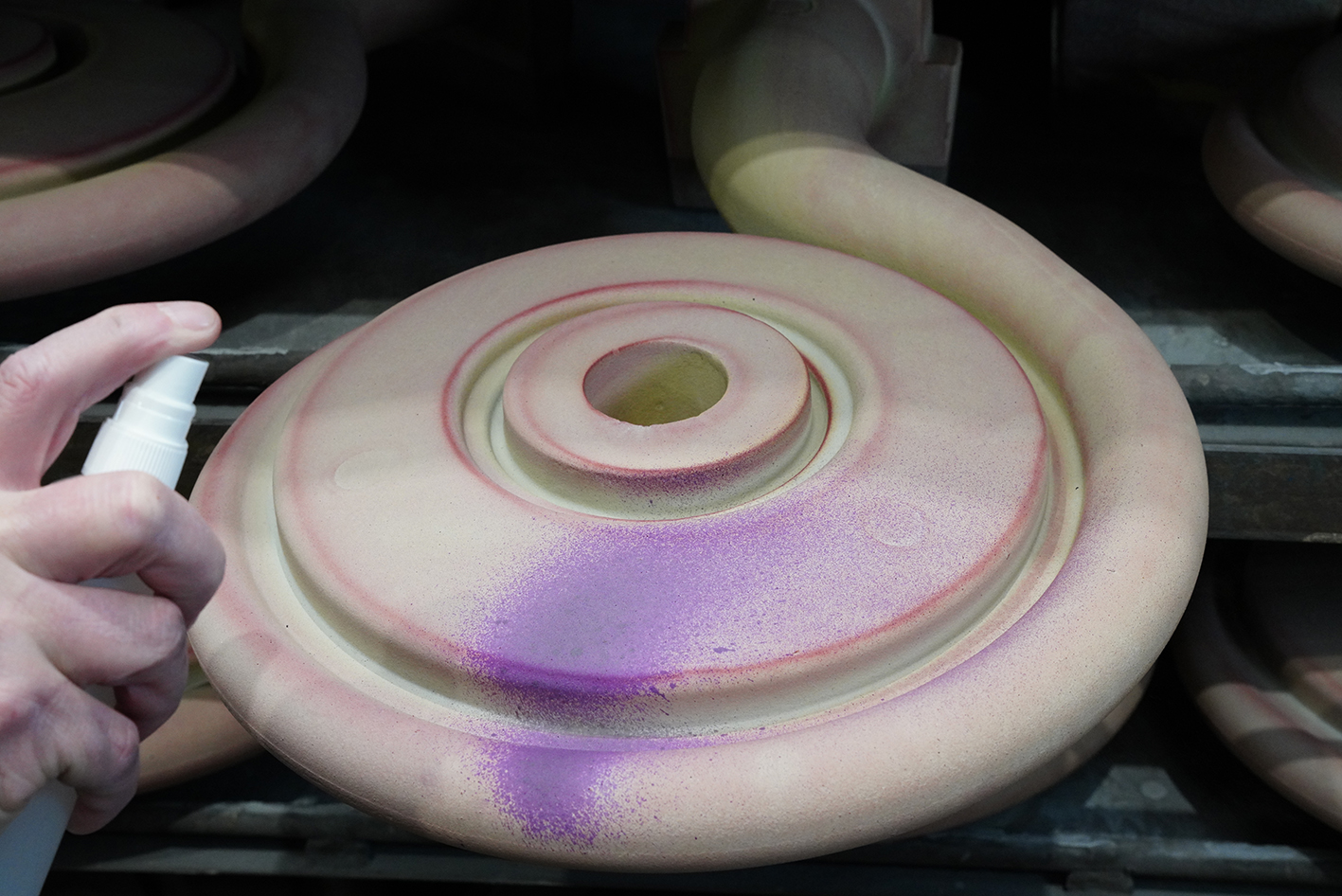
The SEMCO water-based coatings
The SEMCO family of coatings overcomes traditional disadvantages associated with water-based coatings and so extends their use to jobbing foundry applications, which would traditionally use solvent-based alternatives:
- SEMCO FD delivers faster drying rates that are comparable to solvent-based alternatives
- SEMCO CC colour-change-on-drying technology helps optimise the drying process and eliminates the risk that damp moulds will be used
- SEMCO FF reduces evolved formaldehyde emissions
These innovative coatings thus improve foundry efficiency, reduce energy consumption in the drying process, lower harmful emissions, and help cut Scope 2 carbon emissions. Uniquely, these features can also be combined – alongside a choice of filler material – to offer a coating solution tailored to the individual needs of the customer.
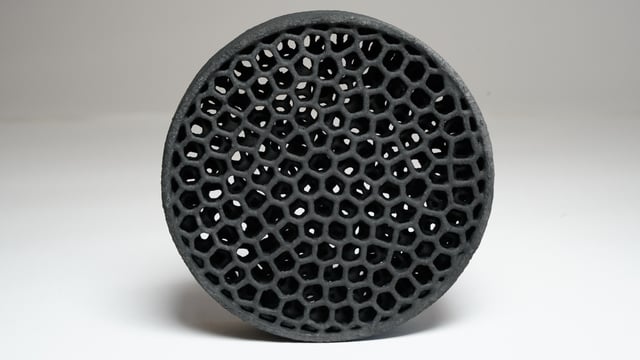
STELEX Optiflow filters for large iron and high-integrity steel castings
We are using the latest 3D manufacturing technologies to extend the range of casting applications suitable for filtration with our STELEX Optiflow3D filters. Initially available with gyroid or Voronoi structure, with a variety of pore sizes, these filters provide the ability to tailor filtration performance for specific castings.
Development is continuing to further assess the performance of the huge range of possible structures and to understand their impact on different casting types and alloys. At GIFA 2023, we will present a range of case studies to demonstrate the application of STELEX Optiflow3D to both iron and steel castings.
These are just some of the innovative products that will be on display at the Foseco stand at GIFA 2023. Visit us in Hall 12, Stand No. 12A02, to discover more and to talk with our team of experts about our latest technologies and continuing innovation work.
Our three themes
- Innovation & Technology
- Sustainability
- Knowledge & Partnership
Sustainability
Find out more about our hihlights in this area.
Knowledge & Partnership
Find out more about our highlights in this area.