STELEX Optiflow3D
Additive manufactured filters for ferrous castings
Additive manufacturing technologies (3D Printing) are enabling a major advance in casting filtration technology. Additive manufacture provides a high level of design freedom; filters will become available with very specific pore sizes, mixed and graduated pores and even a combination of structures in a single filter.
_freigestellt.jpg)
STELEX Optiflow3D Case Study
Case study of a ductile iron cross head casting for a die casting machine, showing how the application of STELEX OptiFlow3D printed filters combined with an SCK Direct Pour led to improved yield, less fettling and reduced costs.
The incorporation of Additive Manufacturing technology (3D) In casting filtration, providing optimised efficiency and customisation
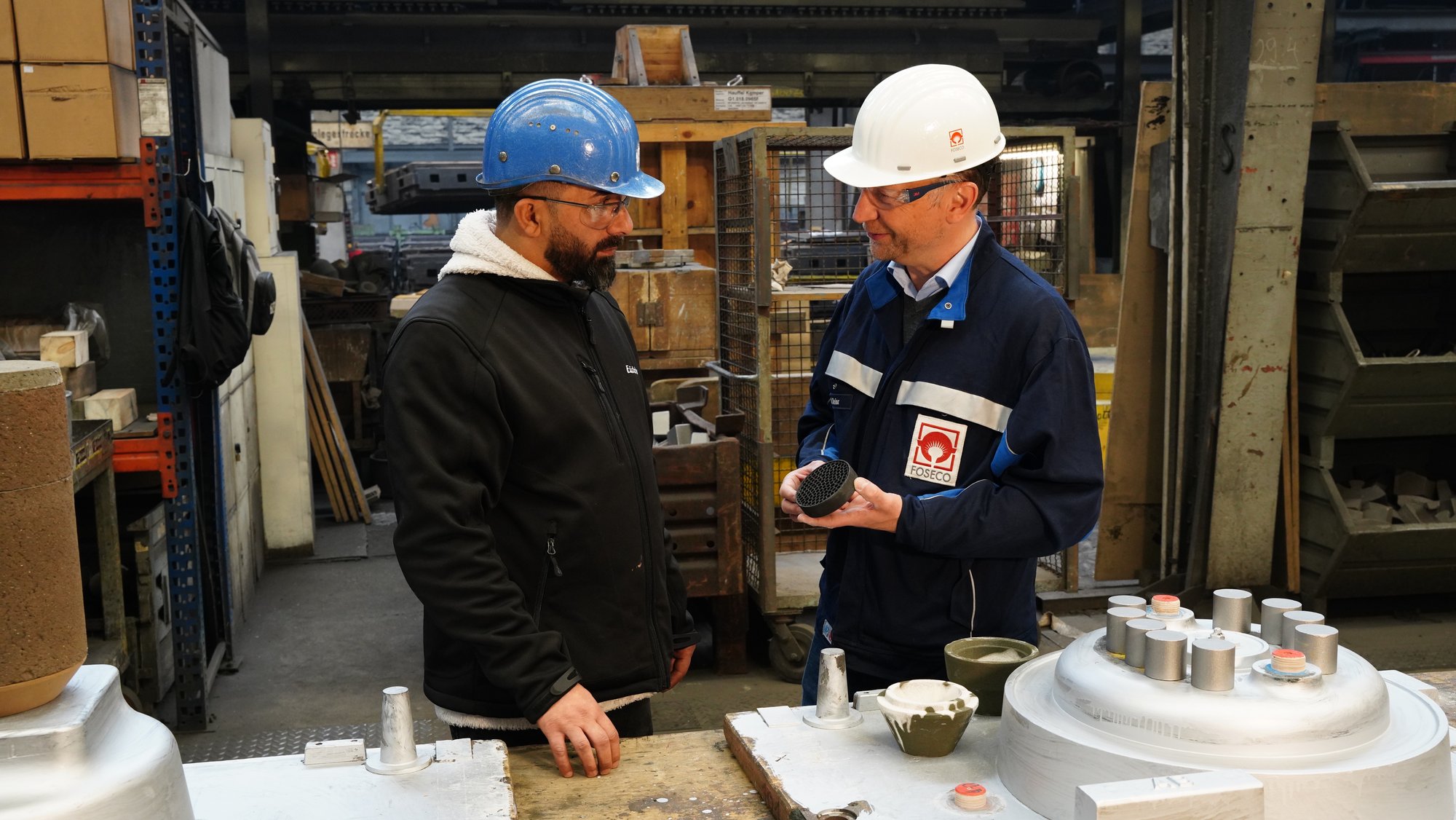
Ceramic foam filters have become the leading choice for metal filtration in casting since the 1980s. They are extensively used across various alloys and casting technologies, providing cleaner castings with improved properties. Over the years, our understanding of filter application has advanced significantly, and guidelines have been developed to ensure their durability. Despite their limitations in pore size and design flexibility, ceramic foam filters outperform other filter types in terms of filtration efficiency and turbulence control. The emergence of additive manufacturing, particularly 3D printing, offers new opportunities for customised filter designs with precise pore sizes and structures, further optimising casting filtration.
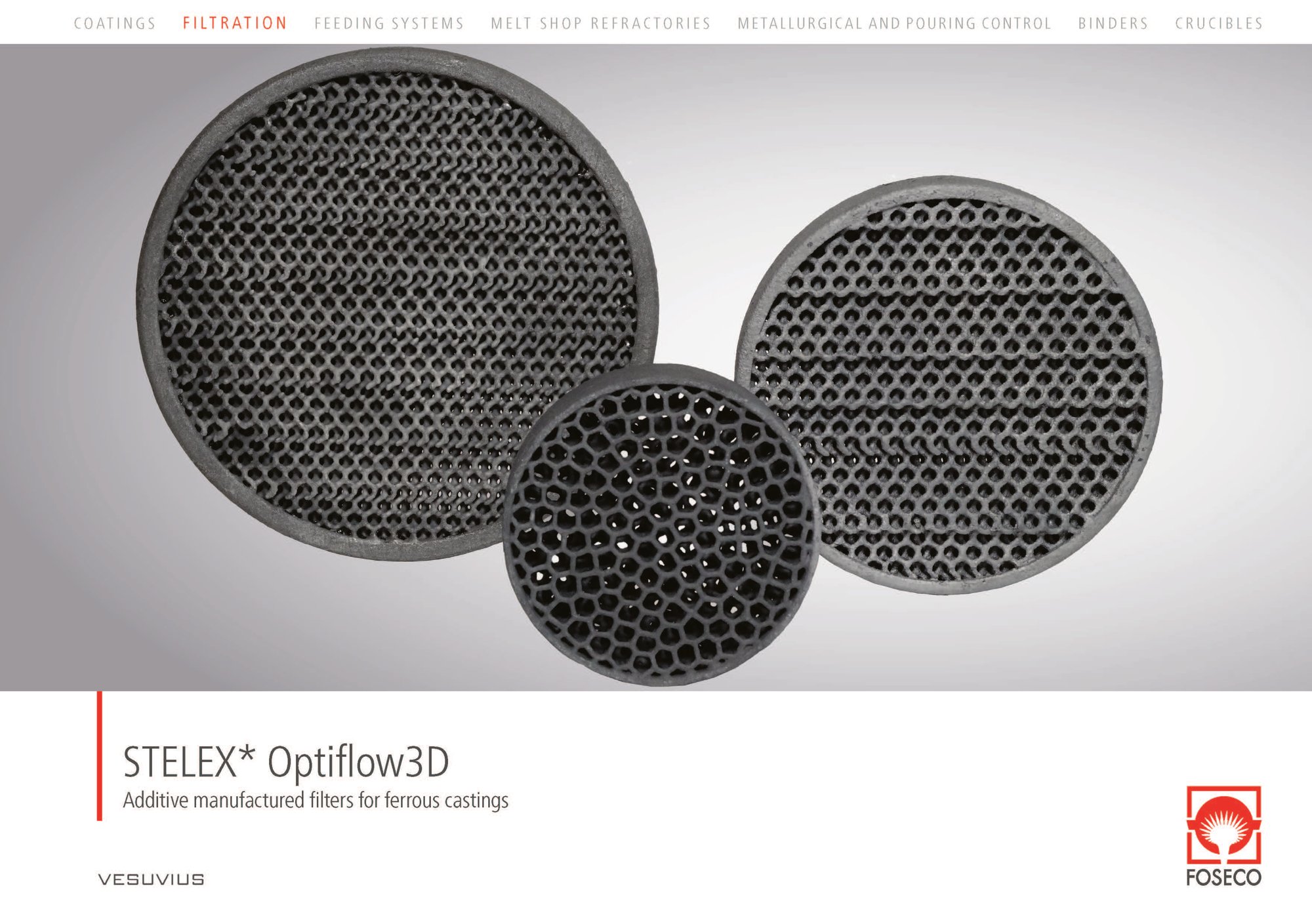
Brochure
STELEX Optiflow3D Brochure
Day 1
Monday 12th June
No video selected
Select a video type in the sidebar.