Customer interviews at GIFA
Weir minerals interviews
Empowering foundry sustainability
Interview with Darren Preece, foundry technical manager at Weir Minerals’ Artarmon foundry in Sydney, Australia.
Döktas interview
A place to find solutions
Interview with Çağri Yamanturk, CTO of Güris Industrial Group (Döktas Foundry), Turkey.
Volvo interview
Achieving the impossible
Interview with Tore Nilsson, Foundry Process Engineer at the Volvo iron foundry in Skövde, Sweden.
Bradken interview
Walking the talk, together
Interview with Stephen Hall, Global Head of Procurement at Bradken, Australia.
Empowering foundry sustainability
Interview with Darren Preece, foundry technical manager at Weir Minerals’ Artarmon foundry in Sydney, Australia.
If you mention environmental sustainability, most will think first about efforts to reduce carbon emissions. But this is only one of the environmental challenges that face the global foundry industry. Another key element is the reduction of waste as part of efforts to promote beneficial re-use of resources, with hazardous waste streams a particular target.
“Switching to more environmentally-friendly consumables – binders and resins, sleeves, hot toppings – is a major focus for us as we work to reduce our environmental footprint by reducing the amount we send to landfill,” explained Darren Preece, foundry technical manager at Weir Minerals’ Artarmon foundry in Sydney, Australia.
“As part of these efforts, we are looking to reduce the amount of fluorides in our sand waste streams to create a less hazardous material that can be re-used in other sectors, such as for asphalt production in the construction industry,” said Preece, who was speaking at the Foseco stand during GIFA 2023.
Weir Minerals are a global supplier of engineered processing solutions for mining and mineral processing applications. The company has produced iron castings at Artarmon since 1969. The foundry utilizes a furane-based sand system to produce parts ranging from 5 kg to 19 tonne as-cast, mainly in high-chromium irons.
Going fluoride free
According to Preece, Foseco has been “instrumental” in this process, supplying Weir Minerals with fluoride-free hot toppings. Artarmon is also planning to implement fluoride-free sleeves in its process. Available in all standard FEEDEX geometries, the Foseco range of FEEDEX FEF and KALMINEX 2000 FF sleeves significantly reduce fluoride emissions and fluoride-containing waste, as well as delivering much lower VOC emissions than market alternatives.
“We expect the fluoride-free sleeves to be a game-changer for us in terms of reducing the fluoride content of our waste sand, and so changing where that waste stream ends up,” continued Preece. “This obviously has a valuable environmental impact; there is also a financial benefit, as our waste sand will no longer be subject to expensive disposal costs.”
“Our fluoride free sleeves are a key milestone on the sustainability journey,” said John Sutherland, International Marketing Services Manager at Foseco. “With our FEEDEX FEF, KALMINEX 2000 FF, and KALMINEX SD products, we now offer a comprehensive range of feeding systems that are either fluoride emission-free or fluoride free, supporting customers as they seek to reduce the use of hazardous materials in their foundries.”
A journey into innovation
Attending GIFA may have required travelling half way around the world. But for Preece it was an important journey to make. “We are a long way from anywhere in Australia! So it is great to have the opportunity to come and get a broader picture of what is available and how we could implement it at Artarmon to improve our operation and product quality.”
Preece already had his eye on some other of Foseco’s latest innovations, notably the HOLLOTEX shroud. Combining the benefits of filtration and shrouding technologies, the shroud facilitates the pouring of large castings, quickly and effectively, without the turbulence that traditionally causes oxide inclusions. “I already have a product in mind, which we are starting to produce patterns for now, where the shroud would be ideal,” said Preece.
A place to find solutions
Interview with Çağri Yamanturk, CTO of Güris Industrial Group (Döktas Foundry), Turkey.
Energy efficiency is the “biggest challenge” facing the foundry industry at the moment, according to Çağri Yamanturk, CTO of Güris Industrial Group, Turkey. The quest for solutions brought Mr Yamanturk and his colleagues to Düsseldorf and to the Foseco stand at GIFA 2023.
.jpg)
Conversion of ductile iron console castings from horizontal to vertical moulding lines through the use of spot feeders
Through its Döktas subsidiary, Güris Industrial Group operates both iron and aluminium casting operations. Its Orhangazi iron foundry is the largest in Turkey and the fourth largest in Europe with a casting capacity of 150,000 tonnes per year. At its Manisa aluminium facility, the company runs high-pressure and low-pressure die casting lines with a total combined capacity of 15,000 tonnes per year.
“Everyone is facing rising energy prices and looking for solutions that improve energy efficiency,” continued Mr Yamanturk. “For us, this means solutions that increase yield. For example, we are working with Foseco on our use of feeders, to improve their efficiency and effectiveness, as well as to optimise their design to our casting needs.” This involves ongoing and frequent collaboration between Döktas and Foseco engineers: “Foseco’s team in Turkey regularly visits our site, working collaboratively with our engineering and production team to implement improvements.”
A case study in partnership
One recent example of the partnership has been the conversion of a large ductile iron casting – which requires spot feeding – from horizontal green sand moulding to vertically-parted moulding. Find out more about this case.
“Our FEEDEX K feeder has enabled Döktas to successfully spot feed an isolated heavy section in the centre of the casting, without modifying the casting geometry or using metal padding to create a feed path,” said Foseco’s Ziya Tanyeli, Business Unit Manager in Turkey. “This effectively allowed the foundry to switch to a vertically-parted moulding line, which reduces manufacturing costs, while still ensuring the soundness of the casting. The application of FEEDEX K feeders also helps to reduce scrap due to shrinkage.”
The Döktas project was one of the featured case studies at the Foseco stand at GIFA and highlights the importance of partnership and knowledge sharing to the future of the foundry industry: a key theme for Foseco at this year’s show.
“We are faced with an operating environment that is increasingly complex and challenging,” continued Tanyeli. “No one company will have all of the answers. Partnership and knowledge sharing will thus be an increasingly important component in the success of the industry moving forward.”
Discovering the latest innovations in foundry technology
Of course, innovation and technology – another key theme of the Foseco stand in Düsseldorf – will also play a critical role in ensuring foundries are equipped to succeed. And catching up with the latest product developments remains a major attraction of GIFA for Mr Yamanturk, his colleagues – and many thousands more. Held every four years, the trade show is the largest trade show for the international foundry industry and, alongside its sister shows, METEC, THERMPROCESS and NEWCAST, brings together the ‘bright world of metals’ from all corners of the globe.
At the Foseco stand, “we were impressed by the ICU Pro intelligent coating unit”, said Mr Yamanturk. By automating the process of controlling, monitoring, and adjusting coating mixes, the ICU Pro ensures coatings are applied consistently, with improved real-time control, process stability, and coating uniformity. The benefits for foundries include optimised drying times, reduced coating consumption, and higher productivity.
“The ICU Pro is the sort of technology that we need in the Turkish metal casting sector,” continued Mr Yamanturk, who noted that the unit on display at GIFA had been sold (on day one of the show) to another Turkish foundry. “It’s good to see the Turkish industry developing and improving through the application of advanced solutions from leading suppliers, such as Foseco. That’s good for the reputation of the sector as a whole, and for the Turkish economy.”
Advances in 3D sand printing had also caught Mr Yamanturk’s eye. “We have been printing cores since 2019, mainly for prototyping and small batch production, so it has been interesting to see the latest developments in that technology here at GIFA.”
Never a wasted trip
“The show is very important for the foundry industry,” explained Mr Yamanturk. “It offers a great opportunity to catch up with our supplies, such as Foseco, to see what they have been developing over the past four years, and to see in which ways the industry is moving. And because it is only every four years, we know that our suppliers have had the time to develop their products and solutions, and so will have something new and interesting to show. It’s never a wasted trip.”
Achieving the impossible
Interview with Tore Nilsson, Foundry Process Engineer at the Volvo iron foundry in Skövde, Sweden.
Tightening environmental regulations are requiring foundries to adopt new and cleaner ways of doing things. That could mean more energy-efficient practices to reduce carbon emissions. Or it might mean switching to consumables that eliminate harmful substances (e.g., formaldehyde or fluoride) in the foundry environment and waste streams. And other times, it means meeting stricter casting specifications from end-users, who themselves are subject to tightening environmental demands.
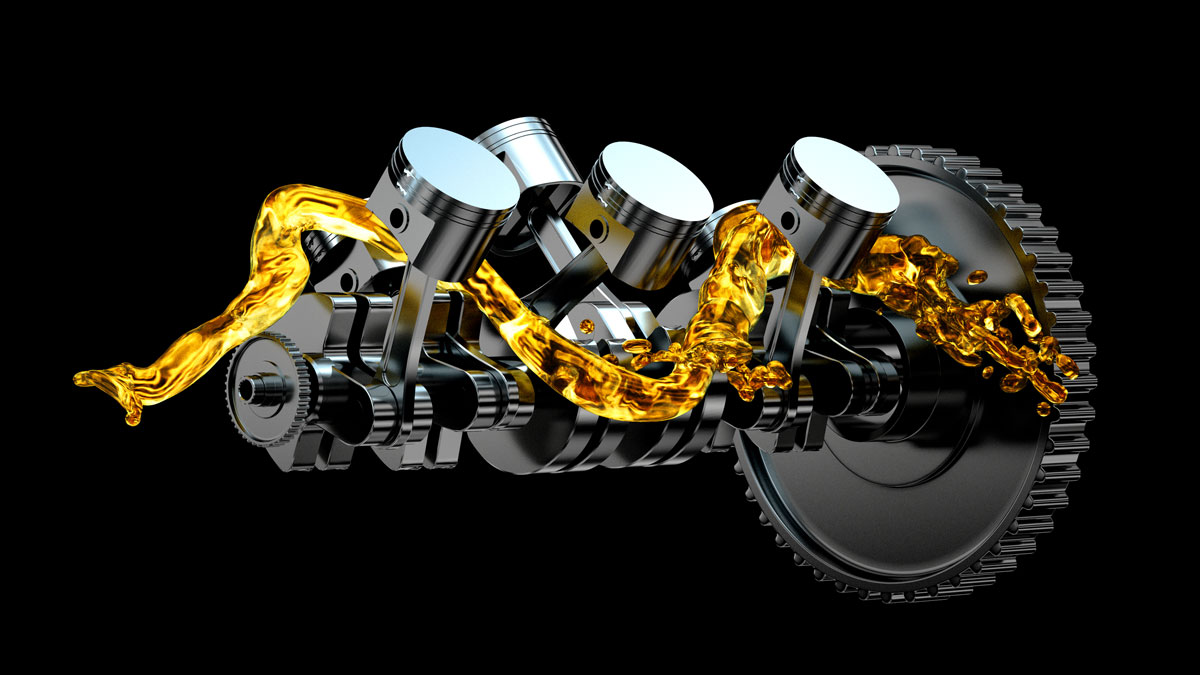
Inner cleanliness coatings for the latest engine technology
The auto industry is a case in point. Electrification is delivering a seismic shift away from the internal combustion engine that will have profound impact on the types of casting required going forward.
But “even as e-mobility is taking off, the combustion engine is going to stay alive for some years yet, especially at the heavier end of the market,” said Tore Nilsson, Foundry Process Engineer at the Volvo iron foundry in Skövde, Sweden. Foundry operations in Skövde date back more than a century. Today, the plant is part of Volvo Group Truck Solutions and supplies the Volvo Group with components for heavy (11-17 litre) diesel engines.
It is however “critical that ICE continue to become cleaner,” continued Nilsson, who was speaking at the Foseco stand at GIFA 2023. This means engines that “operate for longer and more efficiently, and so consume less fuel. To achieve this, we have to achieve tighter tolerances, putting new demands on the castings and casting processes.”
Cleaner (and cleaner) castings
One particular area that Nilsson and his team have been working on is the inner cleanliness of castings to remove as much debris of the casting process (e.g., moulding sand, binder residues) from within complex cast pieces. The specific challenge here came from new EU regulatory restrictions on the use of lead in diesel engines. Lead is traditionally used in engine bearings to achieve satisfactory reliability, acting as a dry lubricant to protect bearings from particulate contaminants. Reducing the number of particulates remaining from the casting process is thus a key enabling factor in phasing out the use of lead.
But reducing particulate contamination also has a beneficial impact on overall engine performance – and thus environmental impact. For example, oil and coolant performance is improved and service life is extended. This raises engine efficiency, as a properly cooled and lubricated engine will run better than an engine with blocked channels.
To meet the inner cleanliness challenge, the Skövde foundry team worked with Foseco to develop the latest generation of SEMCO IC coating. “We have a long history of cooperation with Foseco, going back to the early 2000s,” said Nilsson. “And it has been a very productive partnership. We share our experiences from the foundry side, while Foseco share their knowledge of the products that go into the foundry process. By being transparent and working together, we have been able to develop products that are state of the art.”
Inner cleanliness is a case in point: “It has been an amazing journey with Foseco, getting it to a level that, ten years ago, I would have said was impossible. But we have done it,” continued Nilsson.
A continuing partnership
The SEMCO IC coating – with a video case study from Skövde – was one of 29 new products featured on the Foseco stand at GIFA 2023, which was organised around three key themes: sustainability, innovation and technology, and partnership and knowledge. The themes “represent the future of the industry, guiding discussions throughout the event,” said John Sutherland, International Marketing Services Manager at Foseco. “It was thus a great opportunity to highlight our collaboration with Volvo, which speaks to all three themes in various ways.”
The Volvo partnership with Foseco is also ongoing, with promises of much more to come. “We are currently working with Foseco on a product to significantly reduce the fossil footprint of green sand casting, while also reducing CO2 emissions,” concluded Nilsson. “If we can achieve the sort of results with this new innovation that we did on inner cleanliness, I’m sure it will win all of the environmental prizes at GIFA 2027!”
Walking the talk, together
Interview with Stephen Hall, Global Head of Procurement at Bradken, Australia.
There’s no doubt that the foundry sector is going through some testing times at the moment. Skills shortages. Rising quality expectations. Cost pressures. Decarbonisation… these were just some of the common concerns many visitors raised at GIFA 2023. And while specific solutions abounded on the stands of exhibitors, for one Australian foundry operator, the true value of the tradeshow lay in the potential for strategic partnership.
Bradken is a global producer and supplier of wear-resistant products, primarily mill liners and crawler systems for the mining and minerals processing industry. Founded in 1922, the company has grown over the past century and now operates a global network of foundries with locations in Australia, Canada, China, India, Malaysia, and the US. These cast a range of alloys, including nickel-chromium-molybdenum and chromium-molybdenum irons, white iron, manganese steel, and mild steels.
“We pride ourselves on our customer-centric approach, working with our customers to deliver solutions that meet their needs,” explained Stephen Hall, Global Head of Procurement at Bradken, speaking at the Foseco stand at GIFA. “At the same time, we have a desire to work with suppliers who embody the same values as us.
The quest for partnership
It is this search for partners that brought Hall and his team to Düsseldorf and the largest global gathering for the foundry industry. “Here at GIFA, we are focused on building strategic partnerships with suppliers that have a global footprint and can provide global solutions to address the key issues facing us today,” said Hall. “This means looking at raw materials, equipment, consumables, and processes that deliver a total cost of ownership (TCO) benefit in terms of cost, quality, and sustainability.”
The ultimate aim is to work “more closely with fewer suppliers to deliver the solutions we need,” Hall continued, noting the company currently had more than a hundred suppliers to its sites around the world. Foseco – with its focus on innovation, partnership, and sustainability, as well as its global network of manufacturing facilities – was very much in view. “We’ve had some really constructive conversations here at the Foseco stand at GIFA, and I think there’s a really good opportunity for us to work together on a global stage.”
Partnership was not just on the Bradken team’s mind; it was also one of the key themes of the Foseco stand. “To navigate a way forward, we believe a collaborative approach is needed, with suppliers and foundries working together to find tailored solutions” said Rob Welland, Vice President of Marketing & Technology at Foseco. “It’s great to find a like-minded partner, such as Bradken, and we’re excited about the possibilities for future co-operation on a global scale.”
The sustainability question
Sustainability is one of those issues where partnerships will be key to delivering successful progress. “Bradken’s goal is become carbon neutral by 2030,” explained Hall. “We’re already on the way to achieving this. For example, we have made good progress in sourcing renewable energy contracts for our foundries, with some of our sites now achieving north of 80% sustainable energy. We are now looking at equipment and consumables suppliers and how they can help us meet our net-zero ambition. This been one of the most positive aspects here at GIFA, with many suppliers highlighting their own drive for sustainability.”
Bradken’s sustainability journey aligns with that of Foseco and its parent company, Vesuvius. Sustainability was another of the company’s key themes at GIFA, and its stand was included on the ecoMetals Trail. Organised by trade organisers, Messe Düsseldorf, this highlighted exhibitors that invest in innovative, sustainable, and economically-competitive technologies. Sustainability is also built into Foseco’s approach to business through its strategic sustainability goals. One of these is specifically to help customers reduce their CO2 emissions with products that reduce energy and materials consumption, improve yield and productivity, and reduce scrappage and re-work.
The Foseco stand itself also embodied the company’s attitude to sustainability, being paperless and using recyclable construction materials, when possible. This left a positive impression with Hall. “It’s good to see that, even at this level, when it comes to sustainability, Foseco don’t just talk about it; they’re doing it. This focus and attention to detail is the mark of company that we could do business with.”